The manufacturing process of CNC-Bearbeitung or Computer Numerical Control machining uses computer-controlled machines to create precise parts and components from various materials. The technology has transformed modern manufacturing through its ability to produce complex parts with high precision and repeatability and efficiency for aerospace, automotive, medical and consumer electronics industries. CNC machining operates through pre-programmed software which controls tools and machinery to eliminate human mistakes and boost manufacturing output beyond manual methods.
The Basics of CNC Machining
The fundamental operation of CNC machining relies on computer-controlled tools and machinery through numerical data. A CNC machine uses digital files to interpret instructions which direct the movement of tools and workpieces. The machine receives instructions through digital files which determine its actions for cutting and drilling and milling and turning and grinding operations to transform raw materials into finished parts.
The key components of a CNC system include:
- CNC Machine: The physical equipment, such as a mill, lathe, router, or grinder, equipped with motors and tools to perform specific tasks.
- Controller: The computer or microcontroller that interprets the programmed instructions and sends signals to the machine’s motors.
- Software: Computer-Aided Design (CAD) and Computer-Aided Manufacturing (CAM) software are used to design parts and generate the toolpaths for machining.
- Tools and Workpiece: Cutting tools (e.g., drills, end mills) shape the workpiece, which is the raw material (e.g., metal, plastic, wood) being machined.
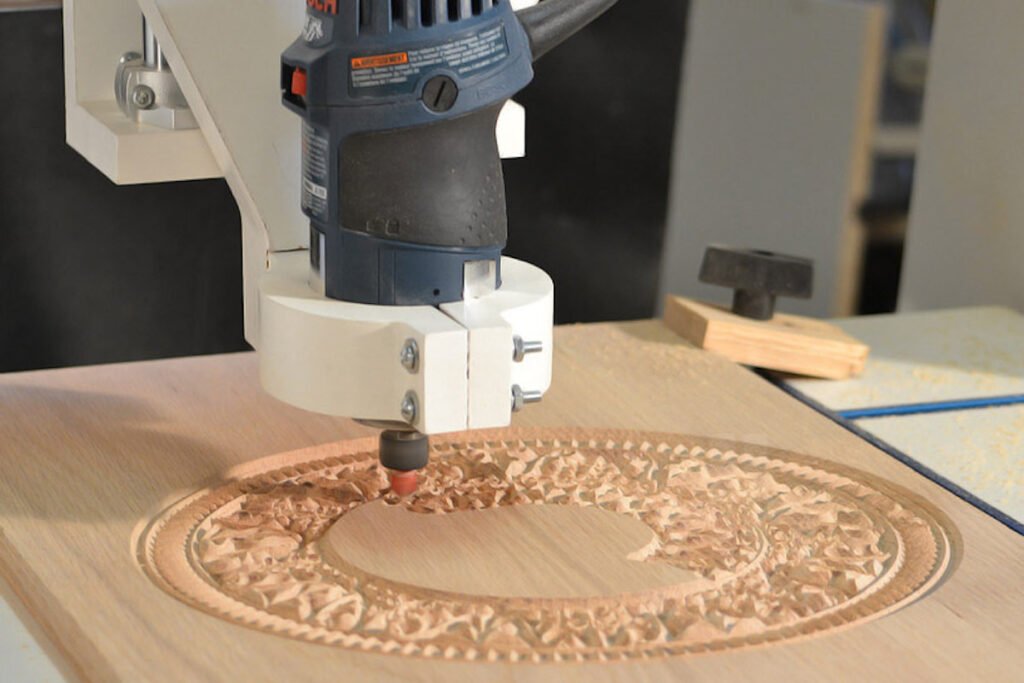
Wie die CNC-Bearbeitung funktioniert
The CNC machining process involves several key steps, from design to finished product. Below is a detailed breakdown of the process:
1. Designing the Part
The process begins with creating a digital model of the part using CAD software. Engineers or designers use CAD to create 2D or 3D models that define the part’s geometry, dimensions, and tolerances. The design includes all necessary specifications, such as hole placements, surface finishes, and material requirements.
2. Converting to Machine Instructions
Once the design is complete, CAM software translates the CAD model into a set of instructions called G-code. G-code is a programming language that tells the CNC machine how to move its tools and workpiece. It includes commands for tool paths, cutting speeds, feed rates, and other parameters. The CAM software optimizes the toolpaths to ensure efficient machining and minimal material waste.
3. Setting Up the CNC Machine
Before machining begins, the operator prepares the CNC machine. This involves:
- Securing the Workpiece: The raw material is clamped or fixed to the machine’s worktable or fixture to ensure stability during machining.
- Installing Tools: The appropriate cutting tools are loaded into the machine’s tool holder or turret.
- Inputting the Program: The G-code is uploaded to the CNC machine’s controller, and the operator verifies the setup to ensure accuracy.
4. Machining the Part
With the setup complete, the CNC machine executes the G-code instructions. The machine’s motors move the tools and workpiece in precise coordination, removing material through processes like:
- Fräsen: A rotating tool cuts material from the workpiece to create flat surfaces, slots, or complex contours.
- Wenden: The workpiece rotates while a stationary tool shapes it, typically used for cylindrical parts.
- Bohren: A rotating drill creates holes in the workpiece.
- Grinding: An abrasive wheel removes small amounts of material to achieve a smooth surface finish.
The CNC machine operates with high precision, often achieving tolerances as tight as ±0.001 inches (0.025 mm), depending on the machine and material.
5. Post-Processing and Quality Control
After machining, the part may undergo post-processing steps such as deburring, polishing, or coating to achieve the desired surface finish or properties. Quality control checks, including dimensional inspections using tools like calipers, micrometers, or coordinate measuring machines (CMMs), ensure the part meets the specified tolerances and standards.
Arten von CNC-Maschinen
CNC technology is versatile and can be applied to various types of machines, each suited for specific tasks:
- CNC-Fräsen: Used for cutting flat and contoured surfaces, slots, and pockets. They typically operate on three to five axes for complex geometries.
- CNC-Drehmaschinen: Designed for turning cylindrical parts, such as shafts and bolts, by rotating the workpiece against a cutting tool.
- CNC-Fräser: Similar to mills but optimized for softer materials like wood, composites, and plastics.
- CNC-Plasma-Schneider: Use a plasma torch to cut through metal sheets, ideal for large-scale cutting.
- CNC Laser Cutters: Employ a laser beam for precise cutting and engraving of materials like metal, plastic, and wood.
- CNC-Schleifmaschinen: Used for precision finishing, creating smooth surfaces and tight tolerances.
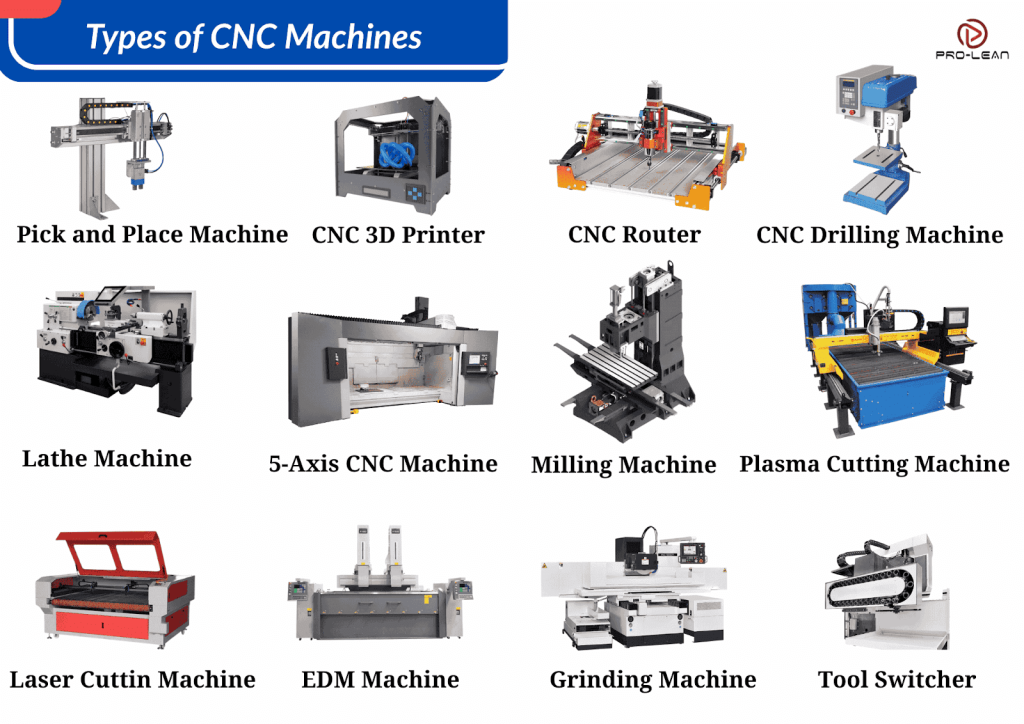
Materialien für die CNC-Bearbeitung
CNC machining is compatible with a wide range of materials, including:
- Metalle: Aluminum, steel, stainless steel, titanium, brass, and copper.
- Kunststoffe: Acrylic, polycarbonate, nylon, and PTFE.
- Verbundwerkstoffe: Carbon fiber, fiberglass, and reinforced plastics.
- Holz: Hardwoods, softwoods, and plywood.
- Foam and Other Materials: Used for prototyping or specialized applications.
The choice of material depends on the part’s application, strength requirements, and environmental conditions.
Vorteile der CNC-Bearbeitung
CNC machining offers numerous benefits, making it a preferred manufacturing method for many industries:
- Präzision und Genauigkeit: CNC machines produce parts with tight tolerances and consistent quality.
- Reproduzierbarkeit: Once programmed, the same part can be produced repeatedly with minimal variation.
- Komplexe Geometrien: CNC machines can create intricate shapes that are difficult or impossible with manual machining.
- Wirkungsgrad: Die Automatisierung reduziert die Produktionszeit und die Arbeitskosten.
- Flexibilität: CNC machines can be reprogrammed for different parts, making them suitable for both prototyping and mass production.
Limitations of CNC Machining
Despite its advantages, CNC machining has some limitations:
- High Initial Costs: CNC machines and software require significant investment.
- Materialabfälle: Subtractive processes like CNC machining remove material, which can lead to waste compared to additive manufacturing methods like 3D printing.
- Skilled Operators Required: Programming and setup demand technical expertise.
- Size Constraints: The size of the workpiece is limited by the machine’s work envelope.
Anwendungen der CNC-Bearbeitung
CNC machining is widely used across industries due to its versatility and precision. Common applications include:
- Luft- und Raumfahrt: Manufacturing complex components like turbine blades and structural parts.
- Automobilindustrie: Producing engine parts, gears, and custom components.
- Medizinische: Creating surgical instruments, implants, and prosthetics.
- Elektronik: Fabricating enclosures, heat sinks, and circuit board components.
- Prototyping: Rapidly producing prototypes for testing and development.
The Future of CNC Machining
Advancements in CNC technology continue to enhance its capabilities. Integration with artificial intelligence (AI) and machine learning is improving toolpath optimization and predictive maintenance. Hybrid manufacturing, which combines CNC machining with additive manufacturing, is gaining traction for creating complex parts with minimal waste. Additionally, advancements in multi-axis machining and automation are expanding the possibilities for producing intricate components with even greater efficiency.
Schlussfolgerung
CNC machining is a cornerstone of modern manufacturing, offering unparalleled precision, flexibility, and efficiency. By leveraging computer-controlled systems, it enables the production of complex parts across a wide range of industries. While it has some limitations, ongoing technological advancements are addressing these challenges, ensuring CNC machining remains a vital tool in the manufacturing landscape. Whether for prototyping or large-scale production, CNC machining continues to shape the future of how we create and innovate.