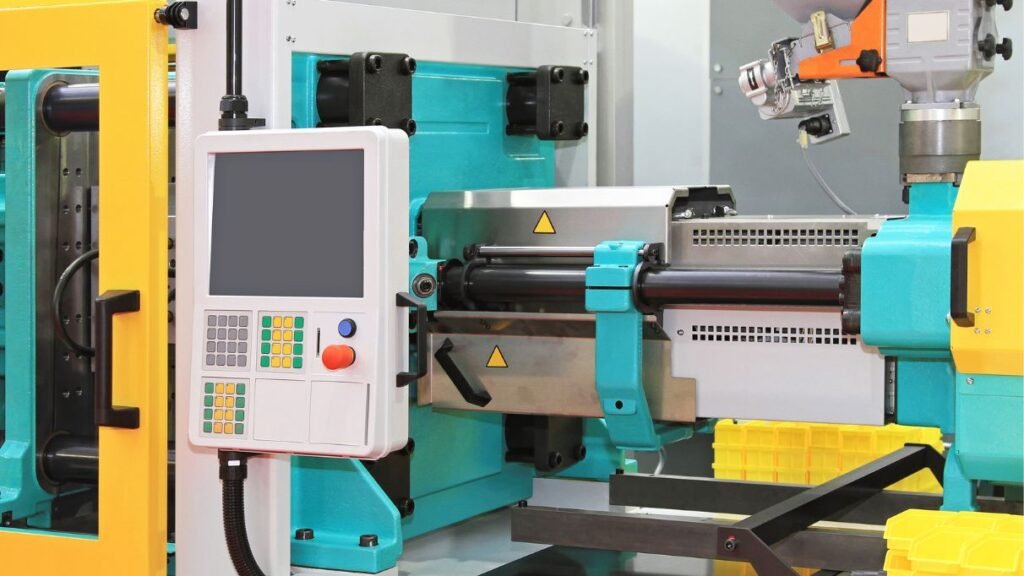
Plastic Injection Mold Making
Let Mekalite help you customize plastic injection molds! Get a quote in as little as 1 hour!
Certifications
ISO 9001:2015 | ITAR Registered | Critical to Quality Inspections
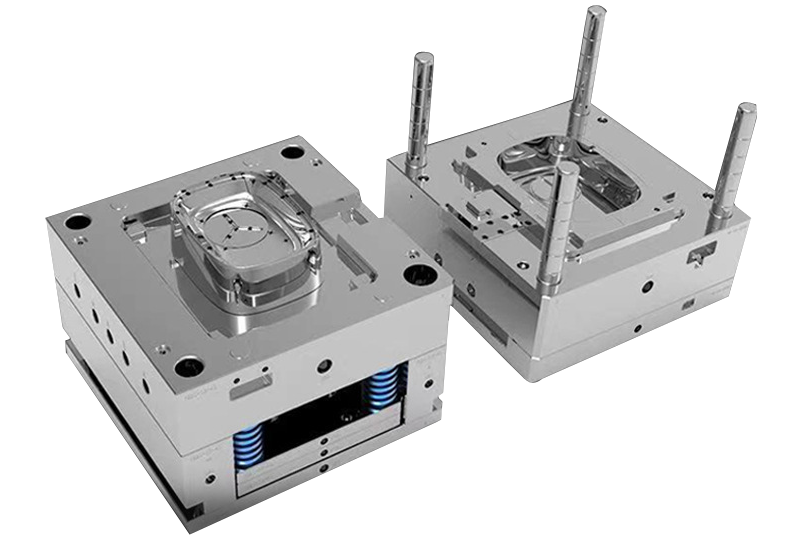
Understanding Plastic Injection Molds
Plastic injection molds are typically made from materials like hardened or pre-hardened steel, aluminum, and beryllium-copper alloy. While steel molds are more expensive, they are preferred for their exceptional durability. Hardened steel molds are heat-treated after machining, offering superior wear resistance and a longer lifespan. Many steel molds are capable of producing over a million parts throughout their lifetime. For lower production volumes, pre-hardened steel molds present a more affordable option, though they are less wear-resistant.
Aluminum molds are a cost-effective alternative but are generally not suited for high-volume production or parts with tight dimensional tolerances. However, they can efficiently produce tens of thousands to hundreds of thousands of parts when designed using CNC machining or Electrical Discharge Machining (EDM).
Copper alloy inserts may be used in specific areas of a mold that require rapid heat removal, which can help reduce cycle times and enhance the aesthetic quality of the final product.
How Are Plastic Injection Molds Made?
Molds are primarily constructed through two methods: standard machining and electrical discharge machining (EDM).
Standard/CNC Machining
In traditional forms, standard machining involves manual operations with lathes, milling machines, and drill presses. With advancements in technology, CNC machining has become the leading method for creating complex and accurate molds. CNC uses computers to control the movement of mills, lathes, and other cutting machines.
In modern CNC systems, the mold design and manufacturing processes are highly automated. The mold’s mechanical dimensions are defined using computer-aided design (CAD) software, which then translates into manufacturing instructions through computer-aided manufacturing (CAM) software. These instructions are converted into specific commands for each machine involved in mold creation.
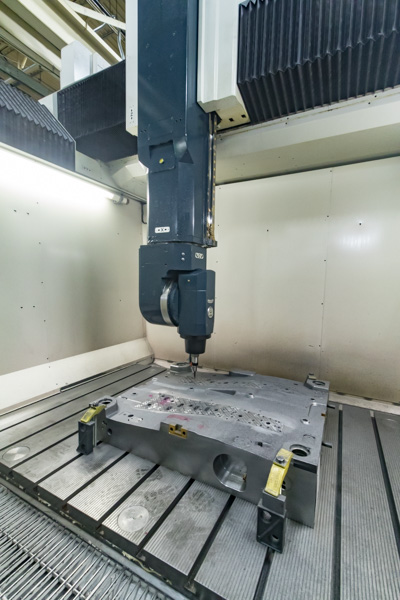
Electrical Discharge Machining (EDM)
EDM is increasingly popular in mold making. This process uses an electrode made from graphite or copper, which is positioned over the workpiece submerged in a dielectric fluid. The electrode is lowered to create a spark gap, allowing controlled electrical discharges to remove metal without direct contact. While this method is slower than conventional CNC machining, it can create complex shapes that are otherwise impossible to achieve.
Additionally, EDM allows for shaping pre-hardened molds without the need for further heat treatment. In some cases, the fine finish produced by EDM serves as the final surface finish for the mold cavity.
Mold Design
A plastic injection mold comprises two primary components: the cavity half (A half) and the ejector half (B half). Here’s how these components work together:
- Plastic Entry: The molten plastic resin enters the A half through a “sprue” or “gate,” sealed tightly by a sprue bushing against the nozzle of the injection barrel.
- Channeling: The sprue bushing directs the molten plastic through channels called “runners,” which are machined into the faces of both the A and B halves of the mold.
- Cavity Filling: The molten plastic flows through the runner and enters specialized gates into the cavity, forming the desired part.
- Ejection: Once the molding is complete, the design ensures that the molded part remains on the B half when the mold opens. The runner and sprue are drawn out of the A half, allowing the part to fall freely from the B half.
A single plastic injection mold can range from having one cavity (producing one part at a time) to multiple cavities, enabling extremely high production rates, as seen in molds designed for items like bottle caps, which can have over 100 cavities.
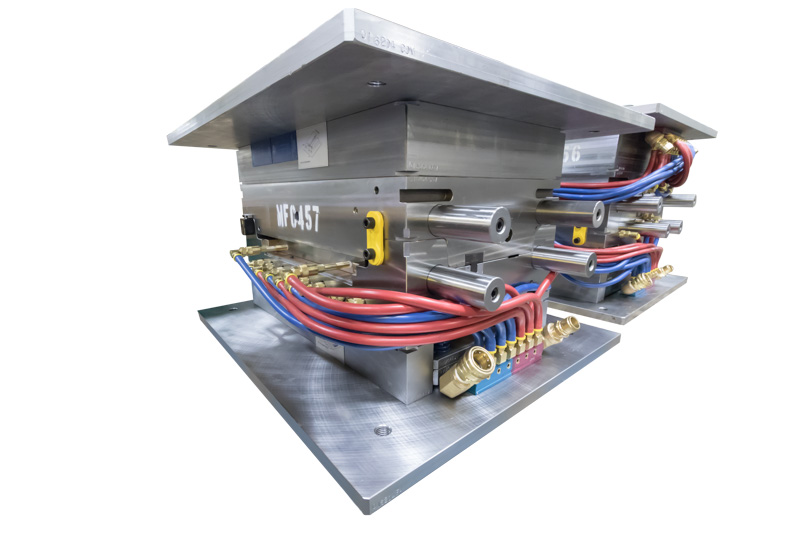