In today’s fast-paced manufacturing world, precision and speed are key. At Mekalite, we’re excited to offer top-notch CNC machining services for our clients. Our advanced facilities and skilled team ensure high quality, quick service, and detailed focus.
Our online platform makes it easy to send designs, get quotes, and track your orders. We use the latest CNC tech to work with many materials, like metals, plastics, and composites. This means we can meet your specific needs.
Need prototypes, small batches, or big production runs? We’ve got you covered. Our services include 5-axis CNC machining, milling, turning, Swiss turning, EDM machining, and precision grinding. We promise quality and satisfaction every time.
Key Takeaways:
- Cutting-edge CNC machining services for precision manufacturing
- Streamlined online platform for design submissions, quotes, and order tracking
- Wide range of material capabilities to meet diverse industry needs
- Comprehensive services from prototyping to full-scale production
- Commitment to quality, efficiency, and customer satisfaction
Understanding CNC Machining: A Comprehensive Overview
The manufacturing world has changed a lot, thanks to CNC technology (computer numerical control). It has changed how we make precise parts. Now, we get better accuracy, consistency, and speed than old ways.
The Evolution of Manufacturing Technology
Before CNC, skilled machinists worked machines by hand. This was slow, hard work and prone to mistakes. But CNC changed everything. Now, machines follow exact plans, making parts fast and accurately.
Basic Principles of CNC Operations
CNC uses special coordinates and computers to guide tools. By using CAD files, CNC machines can cut materials like metals and plastics. This makes complex parts possible.
Key Components of CNC Systems
A CNC system has a multi-axis machine and computer-controlled motors. It works with special software for design and making parts. This setup allows for precise and complex parts, something manual methods can’t do.
CNC has helped many industries like aerospace, medical, and automotive. It lets them make high-quality, custom parts easily. This new way of making parts has changed the game.

“The integration of CNC technology has revolutionized the manufacturing industry, offering unparalleled precision, consistency, and efficiency in the production of specialized components.”
Top 3 CNC Machining Services for 2024
In the fast-changing world of industrial manufacturing, the need for precise CNC machining services is growing. Looking ahead to 2024, we’re excited to offer top-notch CNC machining solutions. These services meet the varied needs of our clients.
Our team of experts excels in 5-axis CNC machining. They deliver unmatched precision and efficiency for custom parts production and industrial manufacturing projects. Whether it’s complex prototypes or large production runs, our CNC milling and turning meet the highest standards.
Our best CNC services stand out because we work with many materials. This includes aluminum alloys, copper alloys, stainless steel, titanium, and plastics. Our flexibility helps us handle complex manufacturing challenges, ensuring our machining providers meet your project’s unique needs.
We’re committed to quality, following a strict quality assurance process. From design to final inspection, we focus on detail and strict tolerance standards. This ensures your product meets or exceeds your expectations.
Our online platform makes starting projects easy and tracking them simple. This focus on innovation and customer satisfaction sets us up to lead in CNC machining services for 2024 and beyond.
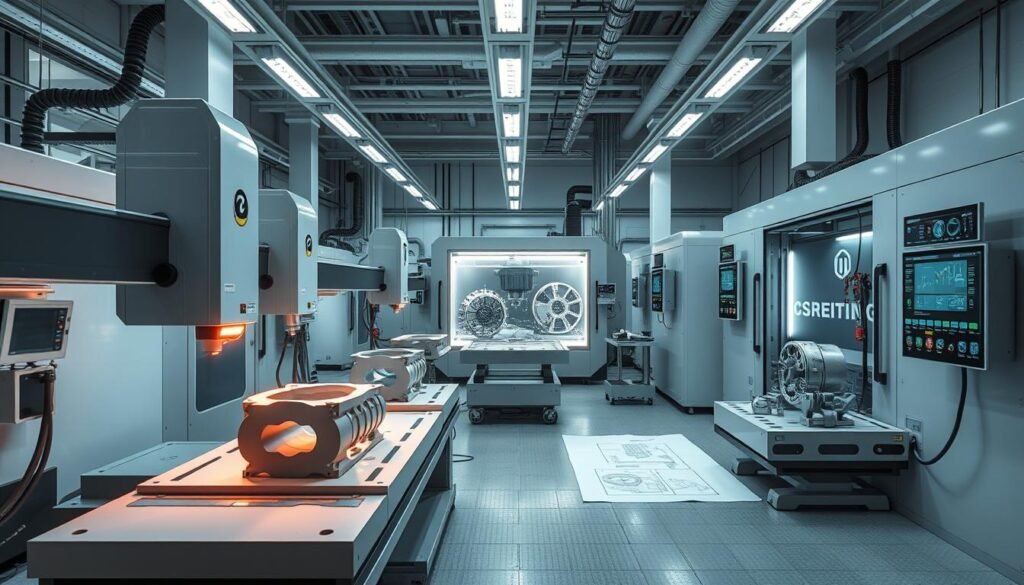
“Their attention to detail and commitment to quality is unparalleled. We’ve entrusted them with some of our most complex projects, and they’ve consistently exceeded our expectations.”
– John Smith, Manufacturing Manager, ABC Corporation
Advanced CNC Machining Processes and Capabilities
At our cutting-edge facility, we provide a variety of CNC machining processes. These meet the high standards of our clients. Our main strength is 5-axis machining. It lets us create complex shapes with unmatched precision and speed.
Multi-Axis Machining Technologies
Our 5-axis CNC machines can work on five axes at once. This opens up new possibilities in high-precision manufacturing. It means we can make detailed parts with great accuracy. This cuts down on extra steps and shortens wait times.
Precision and Tolerance Standards
Precision is key for us, and we aim to meet the strictest tolerance standards. Our skilled team focuses on every detail. They achieve tolerances as small as +/-0.005mm for metals and +/-0.010″ for plastics and composites.
Surface Finishing Options
We also offer a wide range of surface finishes. This ensures your parts look and function perfectly. From basic finishes to custom ones, we can meet your exact needs.
Machining Capability | Specification |
---|---|
Maximum Part Size (Milled) | 80″ x 48″ x 24″ |
Maximum Part Size (Lathe) | 62″ length, 32″ diameter |
Tolerance Capability (Metals) | +/- 0.005mm |
Tolerance Capability (Plastics/Composites) | +/- 0.010″ |
Surface Finish | 125 Ra or better, custom finishes available |
Our advanced 5-axis machining and focus on precision and surface finishing make us a top choice. We’re the go-to for high-precision manufacturing needs in various industries.
“We take pride in our ability to push the boundaries of what’s possible in CNC machining, delivering parts that exceed our clients’ expectations.”
Material Selection Guide for CNC Machining
Choosing the right material for CNC machining is key. We have a wide range of options, including metal alloys and engineering plastics. Each has its own special properties for different uses.
We offer many metals, like aluminum alloys (6061, 5052, 2024, 7075) and copper alloys. We also have brass, stainless steel (303, 316, 17-4), and titanium. Each metal is perfect for certain machining needs.
Our engineering plastics include ABS, acrylic, Delrin, HDPE, nylon, polycarbonate, PEEK, and ULTEM. These plastics have great properties like high temperature resistance and low friction.
Material | Key Properties | Typical Applications |
---|---|---|
Aluminum 6061 | Versatile, good strength-to-weight ratio, easy to machine | Automotive parts, aerospace components, general machining |
PEEK | High temperature and chemical resistance, excellent mechanical properties | Aerospace, medical devices, oil and gas equipment |
Stainless Steel 316 | Corrosion-resistant, durable, suitable for high-precision applications | Food processing equipment, medical instruments, marine applications |
Our experts can help you choose the best machining material for your project. We make sure your product meets your needs and budget.
“The right material selection can make or break a CNC machining project. Our expertise helps ensure the perfect fit between your requirements and the properties of the materials we offer.”
CNC Milling vs. Turning: Understanding the Differences
In CNC machining, CNC milling and CNC turning are key processes. They both offer high precision but are best for different parts and needs.
Milling Applications and Benefits
CNC milling uses tools that rotate to remove material. It works in 3-axis or 5-axis systems. This method is great for making complex shapes and detailed features. It’s often used in aerospace, automotive, and medical fields.
- Versatile for parts with many features on different sides
- Good for detailed patterns, textures, and surface finishes
- Works well with metals, plastics, and composites
Turning Specifications and Uses
CNC turning uses tools on rotating workpieces for cylindrical parts. It works on two axes (X and Z). This makes it perfect for symmetrical, rounded parts. It’s used in automotive, machinery, and consumer goods.
- Great for parts with uniform, cylindrical shapes
- Good for making lots of parts with tight tolerances
- Can achieve smooth finishes and precise dimensions
Choosing the Right Process
Choosing between CNC milling and turning depends on your project’s needs. This includes part geometry, material, precision, and volume. Our team can help pick the best process for your project.
Criteria | CNC Milling | CNC Turning |
---|---|---|
Part Geometry | Complex shapes, contours, and intricate features | Symmetrical, cylindrical parts |
Material | Metals, plastics, and composites | Primarily metals and some plastics |
Precision | Excellent for tight tolerances and detailed finishes | Highly precise for cylindrical parts |
Production Volume | Suitable for low to medium production runs | Efficient for high-volume, repetitive parts |
“Understanding the unique capabilities of CNC milling and turning is crucial for optimizing your manufacturing process and delivering high-quality parts that meet your specific requirements.”
Quality Control and Inspection Methods
At our CNC machining facility, quality is our top priority. We are dedicated to precision and follow strict manufacturing standards. Our quality control process ensures every part meets the highest quality assurance, precision measurement, and inspection techniques standards.
We start by reviewing technical drawings and specifications carefully. We use advanced metrology equipment like coordinate measuring machines (CMMs) and optical comparators. This helps us check the accuracy of every component. Our skilled technicians follow strict manufacturing standards to maintain consistent quality.
- In-process inspections: We check parts at key stages of CNC machining to catch any issues early.
- Final inspection: Before shipping, we do a detailed final check. Our quality team ensures parts meet tolerances and surface finish requirements.
- Comprehensive documentation: We give detailed inspection reports and certificates of conformity for every order. This gives our clients peace of mind that their parts are made to the highest standards.
Inspection Technique | Measurement Capability | Tolerance Range |
---|---|---|
Coordinate Measuring Machine (CMM) | ±0.005 mm | ISO 2768-1 medium |
Optical Comparator | ±0.002 mm | ISO 2768-1 fine |
Surface Roughness Tester | Ra 0.4 μm | ISO 1302 |
Our dedication to quality is the core of our CNC machining services. We use strict inspection techniques and follow strict manufacturing standards. This ensures every part we make meets or exceeds our clients’ expectations for quality assurance and precision measurement.
Cost Considerations and Pricing Structures
Understanding CNC machining costs is key for businesses looking to save money. At our company, we’re all about being open and working with our clients to get them the best deal. This way, they get great value for their money.
Factors Affecting Machining Costs
Several things can change how much CNC machining costs. These include the material used, how complex the part is, and the needed tolerances. Also, the surface finish and how many parts are needed play a role. We consider these carefully to offer prices that are both good and affordable.
Budget Optimization Strategies
We suggest a few ways to save money, like designing parts for easy making, choosing the right materials, and making batches when it makes sense. Our online system gives quick prices for common parts. For more complex projects, our team can give custom quotes.
We aim to find the best way to save money without sacrificing quality or performance. Our focus on CNC machining costs, pricing factors, cost-effective manufacturing, and production efficiency helps our clients meet their goals while keeping costs down.
“We understand that cost is a critical factor in manufacturing decisions, which is why we work diligently to provide transparent and competitive pricing structures for our CNC machining services.”
Pricing Factor | Impact on Cost |
---|---|
Material Choice | Higher-cost materials, such as exotic alloys or specialized plastics, can increase machining costs. |
Part Complexity | Complex geometries, tight tolerances, and intricate features require more time and specialized tooling, resulting in higher costs. |
Production Volume | Larger production runs can often benefit from economies of scale, leading to lower per-unit costs. |
Surface Finish | Increased surface finish requirements, such as polishing or specialized coatings, can add to the overall machining costs. |
Industry Applications and Case Studies
CNC machining is key in many industries. It shows how versatile and useful it is. From aerospace to medical, our CNC work has been crucial in solving specific problems.
In aerospace, we make precise parts for planes and space vehicles. We follow strict standards. Our work in aerospace shows our skill in making custom parts.
The medical field also benefits from our CNC work. We make precise surgical tools and implants. Our focus is on safety and function. Our medical case studies show how we tackle tough challenges.
In the automotive world, we help with prototypes and parts for engines and transmissions. Our work shows we can meet the fast pace of this industry. Our automotive case studies highlight our success in improving performance.
Our CNC services show our dedication to innovation and quality. We handle everything from prototypes to large orders. We’re ready to meet our clients’ varied needs.
Industry | CNC Applications | Case Studies |
---|---|---|
Aerospace | High-precision components for aircraft and spacecraft | Delivering custom parts that meet stringent industry standards |
Medical | Surgical instruments and implant components | Prioritizing patient safety and functionality |
Automotive | Prototypes and production parts for engines and transmissions | Enhancing performance and reliability with custom parts |
“Our CNC machining services have consistently demonstrated our commitment to innovation, precision, and customer satisfaction.”
Common Challenges and Solutions in CNC Machining
In CNC machining, makers often hit technical hurdles that need creative fixes. These hurdles range from tight tolerances to tool wear. Success comes from knowing these problems and finding ways to solve them.
Technical Limitations
One big challenge is the smallest size that can be made reliably. This size varies based on the machine and material. Also, part size is limited by the machine’s work area. Our team keeps machines in top shape to beat these limits.
Troubleshooting Guide
- Surface Finish Imperfections: Poor tool sharpness or wrong cutting settings can cause bad finishes. We keep tools sharp and adjust settings for the best results.
- Dimensional Inaccuracies: Part size errors come from heat, tool bending, or clamping issues. We fix these with precise machine checks, tool choices, and special clamping.
- Material-Specific Machining Challenges: Each material needs its own approach for the best results. We stay updated on how to work with different materials.
We lead in CNC machining tech and keep improving our methods. This lets us beat technical hurdles and make parts that meet tough standards.
Challenge | Solution |
---|---|
Minimum Feature Size | Advanced machine calibration and maintenance |
Maximum Part Dimensions | Optimized work envelope and cutting strategies |
Surface Finish Imperfections | Regular tool maintenance, cutting parameter optimization, and material analysis |
Dimensional Inaccuracies | Comprehensive machine calibration, tool selection refinement, and innovative fixturing techniques |
Material-Specific Machining Challenges | Continuous process knowledge and equipment capability updates |
“By staying at the forefront of CNC machining technology and continuously refining our processes, we are able to overcome technical limitations and deliver high-quality, precision-engineered parts that meet even the most demanding manufacturing requirements.”
Conclusion
At [Company Name], we provide top-notch CNC machining services. We focus on precision, efficiency, and reliability. Our services range from prototyping to full-scale production, meeting various industry needs.
Our team uses advanced technologies and is committed to quality. This means we offer superior manufacturing solutions for complex parts and assemblies.
Our online platform makes ordering easy. Our dedicated support ensures your project’s success from start to finish. Choosing our CNC machining services means you get high-quality results, fast service, and solutions made just for you.
We aim to lead in the CNC machining industry. We’re always improving and adding new services to meet our clients’ changing needs. Explore how our CNC machining services can transform your business.
FAQ
What CNC machining services do you offer?
We provide a wide range of CNC machining services. This includes 5-axis CNC machining, CNC milling, and CNC turning. We also offer Swiss CNC turning, EDM machining, and precision grinding. Our services are for various industries, making custom prototypes and parts quickly and with high precision.
What materials do you work with for CNC machining?
We work with many materials for CNC machining. These include metal alloys like aluminum, copper, and stainless steel. We also work with engineering plastics such as ABS and nylon. Each material has unique properties for different uses.
What are the key differences between CNC milling and CNC turning?
CNC milling uses rotating tools to remove material, often in 3-axis or 5-axis systems. It’s great for complex shapes. CNC turning uses single-point tools on rotating workpieces, mainly for cylindrical parts. The choice between milling and turning depends on the part’s shape, material, needed precision, and how many parts are needed.
How do you ensure quality and precision in your CNC machining services?
We ensure quality and precision through strict quality control. We use high-precision tools and advanced metrology equipment. We follow ISO 2768 standards for tolerances and can meet tighter tolerances as needed.
What factors influence the cost of CNC machining?
Many factors affect CNC machining costs. These include the material, part complexity, tolerances, surface finish, and production volume. We offer competitive prices that balance quality and cost. Our team can give personalized quotes for complex projects.
What are some common challenges in CNC machining, and how do you address them?
Common challenges include tight tolerances, tool wear, and production efficiency. We solve these with advanced machine calibration, regular tool maintenance, and smart cutting strategies. Our guide helps with issues like surface finish problems, dimensional errors, and material-specific challenges.