At Mekalite, our core mission is precision. We expertly bridge the art and science of injection mold design to serve the ever-evolving demands of industries worldwide. Our relentless pursuit of perfection in custom mold manufacturing is underpinned by advanced CNC machining technologies and elevated by our unwavering commitment to craftsmanship. As leaders in mold fabrication, we not only fulfill clients’ visions but exceed them. This is the essence of our approach – blending high-precision tooling with the meticulous nature of a craftsman to forge unparalleled manufacturing solutions.
Client satisfaction hinges on the smallest details — details that we at Mekalite excel at perfecting. We understand that each touchpoint of a mold’s design plays a critical role in the end product’s performance. That’s why we’ve honed our craft to ensure that from conceptualization to realization, every project reflects our dedication to quality and precision in injection mold design and mold fabrication.
The Rise of Precision Injection Mold Making
In the dynamic world of manufacturing, the push towards technological innovation has significantly elevated the standards and capabilities of high-precision injection molding. This meticulous process is instrumental in enhancing manufacturing efficiency and meeting the sophisticated demands of modern industries.
Advancements in Manufacturing Technology
The realm of precision injection molding has transcended traditional boundaries through the integration of advanced technologies. Automation, spearheaded by industry leaders like Mike Cope of Hurco Companies, Inc., plays a pivotal role in optimizing production processes. Automation systems such as pallet loaders and job assignment protocols have reshaped the operational landscape, enabling manufacturers to achieve remarkable increases in production hours and overall efficiency.
Increasing Demand for Precision Components
The necessity for ultra-precise components is escalating across various sectors, notably in medical devices and automotive industries. These sectors require components that conform to exceptionally strict tolerances, often ranging between +/- .002″ and +/- .001″ or even finer. Bill Wood from Plastic News notes that the demand for precise molds is subject to moderate but impactful fluctuations, highlighting the need for manufacturers to remain adaptable and responsive to market changes.
Innovations from Mekalite
At Mekalite, innovation is at the heart of our operations. We utilize cutting-edge equipment and techniques to ensure that our molds not only meet but surpass the intricate design specifications of our clients. Our ongoing commitment to innovation is illustrated by our adoption of durable, advanced materials and our involvement in the latest molding technologies which include the injection of metals, ceramics, and carbides alongside traditional plastics. This adaptability enables us to proficiently address the evolving needs of industries requiring high-performance, corrosion-resistant components.
Moreover, Mekalite is at the forefront of environmentally responsible manufacturing practices. As the industry embraces bio-resins and seeks to reduce the environmental footprint, our efforts are aligned with these sustainable advancements, ensuring that we not only comply with current demands but also contribute positively to the environmental goals of the sector.
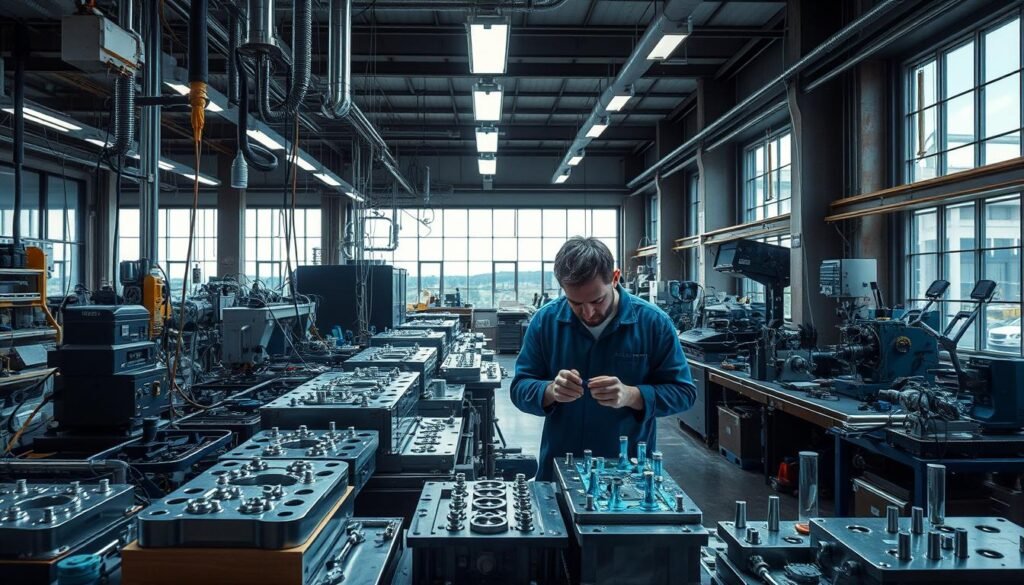
Understanding the intricate dynamics of high-precision injection molding is fundamental for industries aiming to thrive in a competitive market. With our emphasis on technological innovation and manufacturing efficiency, Mekalite remains a stalwart partner to businesses aiming for superior manufacturing outcomes.
Injection Mold Making: The Mekalite Approach
At Mekalite, we delve into the complexities of modern injection mold making through a well-defined and innovative approach. Reflecting our cornerstone principles of precision and craftsmanship, this process begins with understanding client-specific needs and harnessing our robust capabilities in state-of-the-art machinery and custom injection molding. Our method is not only about creating moldings but ensuring they are perfectly tailored to meet the demands of various industries.
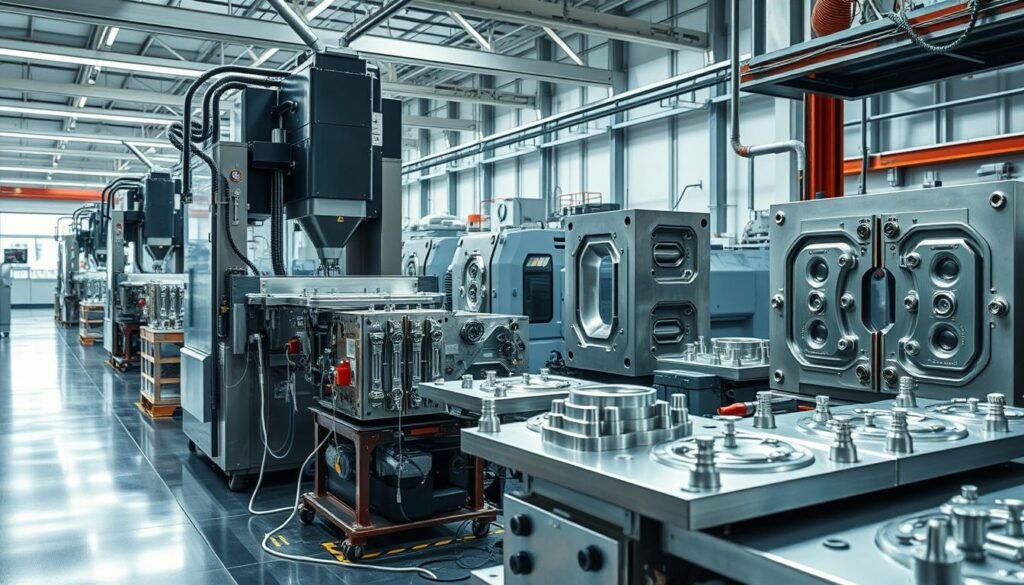
Utilizing Cutting-Edge Equipment
Our facility is equipped with modern CNC machining and EDM technology, essential in producing molds that adhere precisely to specified tolerances. Mekalite maintains a machining tolerance of +/- 0.003 in. (0.08mm), placing us at the forefront of industry-specific molding precision. This capability is supported by our extensive use of aluminum and steel molds, which not only facilitate a quicker production cycle but also are durable enough to handle the demands of large-scale manufacturing.
Remote Support and Operations Assistance
Understanding the ongoing need for operational support, Mekalite incorporates remote monitoring in our service offerings. This feature enables us to provide real-time assistance and immediate troubleshooting solutions, thereby maintaining continuous production without compromising on quality or efficiency. The integration of such innovative solutions underscores our commitment to supporting our clients’ operational needs from afar.
Custom Solutions for Diverse Industries
We pride ourselves on our ability to offer custom injection molding solutions that cater to a wide array of industries. By analyzing specific client requirements, we can adapt our processes to create highly specialized molds. From single to multiple cavity configurations, our molds can manage everything from small batches to mass production schedules effectively, reflecting our versatility and capability in addressing diverse client demands.
Material Capability | Mold Type | Production Capacity | Surface Finishes |
---|---|---|---|
100+ thermoplastic and thermoset materials | Aluminum, Pre-hardened Steel, Copper Alloy Inserts | Up to hundreds of thousands, including one million+ for steel molds | Options like PM-F0 and PM-F1 |
Quality inspections include DFM Feedback and Post-Processing such as Mold Texturing |
Thus, Mekalite’s tailored approach in the art and science of mold making extends beyond the typical boundaries of custom injection molding, blending advanced technology with meticulous operational support to serve the dynamic needs of today’s industries.
Materials and Techniques in Mold Making
In the realm of precision engineering, the choice of materials and techniques plays a pivotal role. At our company, we focus extensively on material selection and mold design techniques to ensure that every product aligns with the stringent criteria of precision engineering. These efforts are complemented by our commitment to innovative molding solutions, ensuring top-tier quality in all projects.
The material selection process is guided by several criteria, including the desired properties of the end product, the expected production volumes, and environmental considerations. Different materials offer varied benefits, such as thermal stability, strength, and aesthetic finishes. For instance, using premium resins like polycarbonate or ABS can significantly affect the durability and appearance of the final product.
Moreover, our mold design techniques are refined to accommodate specific production needs, from single-cavity molds for low-volume production to complex multi-cavity molds for high-throughput requirements. Here, precision is key, and our designs ensure that each mold meets exact specifications with tolerances as tight as ±0.003 inches.
- Precision in Production: Our molds maintain a shrink tolerance range that varies depending on the resin used, ensuring the precision of the end components.
- Structural Integrity: Recommendations for wall thickness are rigorously followed to ensure that parts maintain structural integrity without excessive use of material.
- Design Specifications: Draft angles and rib thicknesses are meticulously calculated to prevent defects such as warping or sinks during the molding process.
Material | Recommended Wall Thickness | Typical Shrink Tolerance |
---|---|---|
ABS | 40%-60% of adjacent wall | 0.002 in./in. |
Polycarbonate | 40%-60% of adjacent wall | 0.002 in./in. |
TPE | 40%-60% of adjacent wall | 0.025 in./in. |
Through the integration of advanced materials like carbon fiber and the implementation of sophisticated mold design techniques, our innovative molding solutions push the boundaries of what is possible in precision engineering. This holistic approach not only enhances the durability and performance of the final products but also significantly optimizes the production process, ensuring cost-efficiency and high-quality outputs.
As we continue to refine our methodologies and implement cutting-edge technologies, our goal remains clear: to deliver unmatched quality and precision that exceed expectations every time.
Case Studies: Mekalite’s Track Record
At Mekalite, our commitment to manufacturing excellence is evident through our portfolio of successful molding projects. These case study insights are not merely a testament to our capabilities but a clear indication of our unwavering dedication to quality assurance and precision in manufacturing. Below, we delve into specific examples that illuminate our track record.
Industry | Project Description | Technology Used | Outcome |
---|---|---|---|
Aerospace | Custom components for aircraft | CNC Milling, EDM | Components delivered with precision up to +/- 0.01 mm |
Military | Intricate components for military hardware | Advanced CNC turning and milling | Enhanced durability and exact compliance with military standards |
Medical Devices | Prototypes for surgical instruments | EDM, CNC Lathe | High precision prototyping that led to successful product launches |
Electronics | Enclosures for high-end electronic devices | CNC Router, CNC Grinder | Efficient production with exceptional material finish and fit |
Focusing on detailed case study insights from each sector has allowed us to refine our process continually. We leverage state-of-the-art technology like CNC Mills, Lathes, and EDM machines to ensure each project meets the rigorous standards expected in highly regulated industries such as aerospace and medical devices. This approach is central to maintaining our reputation for manufacturing excellence.
- Successful molding projects with top American aerospace and military firms, showcasing our advanced machining capacities.
- Comprehensive quality assurance processes that begin with material selection and extend through to final quality checks.
- Dedication to manufacturing excellence, utilizing advanced technologies like CNC machining for intricate and precise designs.
We are committed to upholding the highest standards of service and production. Through detailed analytical approaches and improvements to our CNC machining processes, the successful completion of complex precision projects is a promise we give and deliver to each customer.
Conclusion
At the core of precision mold making is an unyielding commitment to quality and customer-focused service. We, at Mekalite, rigorously apply this ethos throughout our manufacturing partnerships, ensuring every project aligns with our clients’ specific needs and quality standards. Precision mold making not only facilitates the production of exact parts but also enhances the efficiency and outcome of mass production, making it a focal point of our operations.
In this competitive space, the automation of the injection molding process stands out as a significant advancement, reducing the need for manual labor while simultaneously increasing productivity. This efficiency is particularly prominent when addressing high-volume production needs. Mekalite harnesses this efficiency by implementing cutting-edge technologies that cater to a diverse range of materials and complex designs.
Furthermore, the consideration of tooling costs and design flexibility speaks directly to our adaptability and solution-oriented approach. While acknowledging that initial investments in mold tooling are substantial, our strategic planning ensures that these costs are mitigated over the lifespan of the mold through meticulous design and engineering practices.
- Mold varieties such as hot runner and cold runner molds cater to different production requirements.
- Diverse material use—from metals to non-metals—further exemplifies our capability to customize according to application specs.
- Aluminum molds, recognized for cost-effectiveness, are leveraged for less intricate designs, demonstrating our dedication to providing economical solutions.
All these considerations are framed within our broader commitment to delivering precision, quality, and value to our clientele, driving forward our reputation as leaders in the industry.
By building robust manufacturing partnerships, we extend far beyond the typical supplier role, engaging deeply with each project to achieve seamless production processes and superior outcomes. This integrated approach ensures that despite the complexities of precision mold making—be it materials choice, design considerations, or cost-efficiency—our clients receive tailored, high-quality solutions.
At Mekalite, our collaborative efforts reflect a synthesis of expertise, innovation, and practical application in precision mold making. We stand committed to excellence, supporting our clients through every step of the manufacturing process, reinforcing longstanding relationships through trust and demonstrated capability in delivering specialized solutions.
Contact Us
Are you seeking a partner who can provide professional molding consultation and enhance your production with exemplary precision and quality? At Mekalite, our commitment to excellence has been the cornerstone of our services since 1988. Whether your project necessitates the utilization of advanced materials such as ABS, HDPE, PEEK, PET, PVC, TPU, EPDM, PEBA, or LSR, our team is well-equipped to deliver high-strength, resilient components designed to meet rigorous industry standards.
Our customer service team takes pride in understanding the diverse needs of various enterprises, from medical to automotive injection molding. With a strong presence in North Carolina, South Carolina, Pennsylvania, Maryland, Tennessee, Georgia, and Virginia, we are poised to cater to a broad clientele with state-of-the-art presses that offer up to 610 tons of pressure for large-volume production. When you contact Mekalite, you’re not just getting a quote—you’re accessing decades of industry expertise and a partnership that ensures your high-volume orders are not only fulfilled on time but with unmatched precision.
To begin a dialogue about how Mekalite can revolutionize your manufacturing capabilities, we invite you to reach out to us. Our adept team is ready to provide you with a comprehensive professional molding consultation, tailor a quote to your unique specifications, and ensure that the solutions we deliver are aligned perfectly with your objectives. Don’t hesitate, contact Mekalite today and take the first step towards optimizing your production line with our renowned precision injection mold making services. Your success is our craft.
FAQ
What precision injection mold making services does Mekalite offer?
We specialize in precision injection mold design and custom mold manufacturing. Our services harness the precision of high-precision tooling and CNC machining to deliver top-quality mold fabrication to a diverse array of industries.
How has technological innovation impacted Mekalite’s services?
Advancements in manufacturing technology have significantly enhanced our high-precision injection molding capabilities. We’ve adopted state-of-the-art equipment and techniques to improve manufacturing efficiency and meet the increasing demand for precision-engineered components.
Can Mekalite provide operational support for their products?
Absolutely. We offer remote monitoring and operational support services to ensure that our clients’ manufacturing processes run smoothly and efficiently. This is part of our commitment to provide custom injection molding solutions that cater to the specific needs of each industry we serve.
What materials and techniques does Mekalite employ for mold making?
Our team is skilled in selective material selection and employs advanced mold design techniques to ensure each mold meets the precision engineering requirements of our clients. We continually integrate innovative molding solutions for exceptional product quality.
How does Mekalite demonstrate their manufacturing excellence?
We provide detailed case studies as evidence of our successful molding projects. These case studies offer insights into our process and reinforce our dedication to quality assurance and manufacturing excellence.
What makes Mekalite’s approach to client service stand out?
Our approach is customer-focused and characterized by a steadfast commitment to quality. We pride ourselves on forming durable manufacturing partnerships and offering tailor-made solutions that excel in demanding applications.
How can I get professional molding consultation or a quote from Mekalite?
To receive expert advice and a customized quote for your specific needs, simply contact our customer service team. They are prepared to assist you with all your professional molding consultation needs.