Bead Blasting Services
We can effectively remove rust, paint, scale, and other contaminants from various surfaces using bead blasting. Get a uniform and matte finish on surfaces to enhance the aesthetic appeal of the material.
Bead Blasting for Custom Parts
Bead blasting can be controlled to selectively remove material, making it perfect for delicate work on items like jewelry or intricate metal parts.
At Mekalite, precision is our standard. Our advanced CNC machining capabilities ensure that every component we produce meets the highest industry standards. Mekalite uses cutting-edge bead blasting techniques to enhance the quality and finish of your components.
Our skilled team uses fine glass beads to achieve optimal results in surface cleaning, deburring, and finishing. The controlled and gentle nature of our bead blasting process ensures that even the most delicate materials are treated with care. We also offer customizable bead blasting solutions to meet your specific requirements. Whether you need a uniform matte finish or selective material removal, our team is skilled at adapting our processes to suit your needs.
TECHNOLOGY OVERVIEW
More About Anodizing
What’s Bead Blasting?
Bead blasting is a surface finishing technique that cleans or prepares materials by propelling tiny beads at high pressure onto their surfaces. The process involves a blasting setup with a chamber, nozzle, and dust collector.
Using compressed air, beads made of glass, ceramic, or metal are accelerated to remove contaminants like rust or paint, providing a uniform texture. This method is used in automotive and aerospace for tasks like cleaning, deburring, and surface preparation. The choice of bead material and size depends on the material being treated, ensuring a desired finish without causing damage.
Advantages of Bead Blasting
- Removes rust and corrosion
- Improves surface finish
- Enhances paint adhesion
- Cleans and prepares surfaces efficiently
- Versatile for various materials
- Cost-effective
- Eco-friendly option
Design Considerations for Bead Blasting
- Prioritize protective gear, ventilation, and safety interlocks.
- Choose a suitable bead blasting machine based on size, pressure, and abrasive media compatibility.
- Select material and size for desired surface finish and substrate compatibility.
- Implement precise control systems for pressure, media flow, and nozzle adjustments.
- Design an ergonomic workspace with proper lighting and easy maintenance access.
- Install efficient systems to minimize airborne particles for a clean and safe environment.
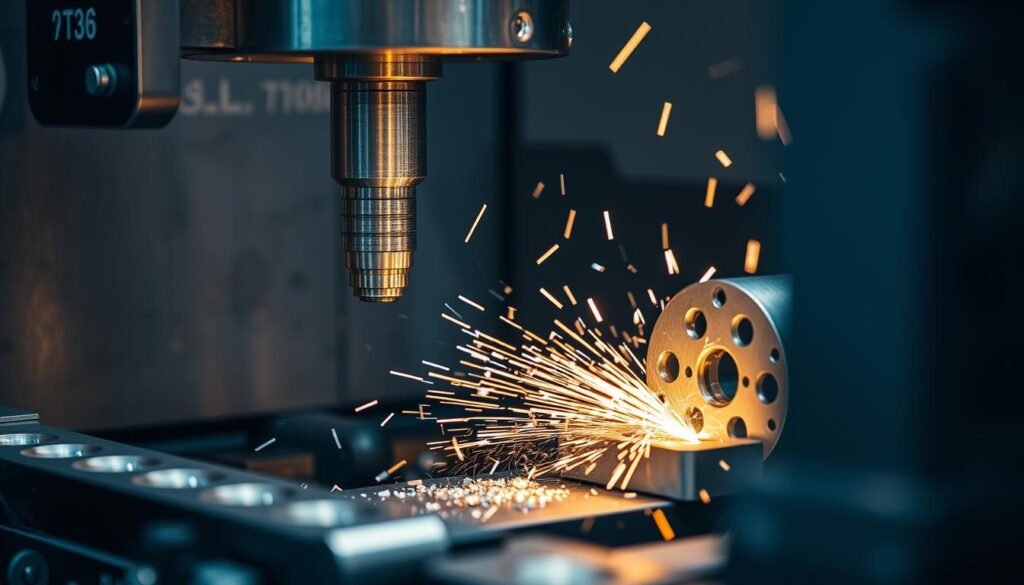
Get An Accurate Quote For Your Next Projects
No matter your project is complicated or simple, no matter is metal or plastic, you will get an accurate quotation within 6 hours.